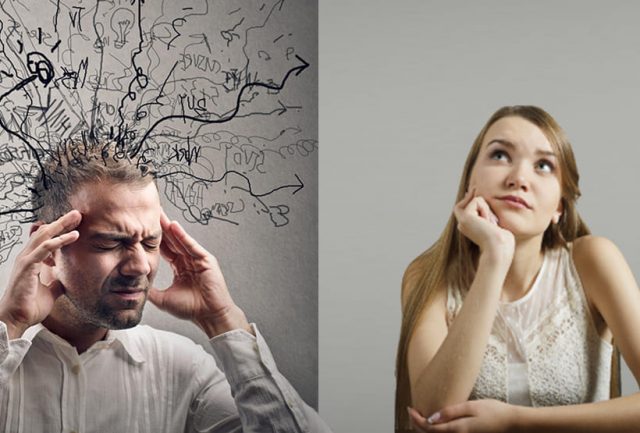
Lean Thinking, cosa non è, un mito da sfatare…
Il Lean Thinking non è una mera metodologia, come spesso la ritengono diverse aziende. L’errore sostanziale consiste nell’immaginare la Lean come un insieme di strumenti e tecniche innovative che, una volta “installate” nel sistema aziendale esistente, possono cambiare, in meglio, la realtà aziendale. Questo approccio è fallimentare, per tre ragioni:
- Perché la Lean non si può concepire come una raccolta di metodologie ma è, innanzitutto, un nuovo modello produttivo che richiede un cambio di paradigma sostanziale.
- Dietro questa forma di retro-pensiero, di fatto, si pensa di delegare, di trasferire il cambiamento ad altri: a dei formatori esterni, a dei coach o ad una società di consulenza.
- Ma ciò che, più di tutto, rappresenta il vero ostacolo è che, pensando e agendo in questo modo si vuole nascondere il fatto che, in fondo, si è convinti che non ci sia nulla da cambiare e che le cose funzionino, tutto sommato, bene così come sono, da sempre, nello stesso modo. Si sente spesso ripetere, infatti: abbiamo sempre fatto così. Il vero problema, sento spesso ripetere dal management, sono le persone che non svolgono in modo proficuo il loro lavoro. Tutt’al più, i manager che pensano in questo modo, sono solamente disposti ad apprendere nuovi metodi, a tentare di mettere in atto altre strategie, ma senza cambiare di una virgola le proprie convinzioni e il proprio approccio. Siccome in altri contesti ha funzionato, si pensa che sia sufficiente ricalcare il solco dell’esperienza compiuta da altre organizzazioni. Vale la pena di tentare…
Cosa può scatenare conoscere il Lean Thinking?
- Si viene a conoscenza dei successi ottenuti in altri contesti aziendali.
- Li si va magari a visitare.
- Si rimane colpiti e incuriositi dai risultati e dall’ambiente circostante che è migliorato.
- Ci si documenta, si intervistano le persone, si chiedono informazioni su chi, dall’esterno, ha guidato il progetto.
- Si discute in sede direzionale sulla possibilità di introdurre gli stessi schemi e dinamiche, al proprio interno.
- Viene effettuata una verifica sulla possibilità ed eventualità di ricorrere a progetti finanziati.
- È possibile contattare società di formazione e consulenza.
- Dopo aver allineato le offerte e si sceglie quella più economica, a parità di contenuti, ponendo molta attenzione ai costi.
- Si definisce e concorda un calendario.
- Si parte con la formazione e con qualche attività ben circoscritta.
E, terminata l’esperienza, il gioco è quasi fatto…
Installare un nuovo modo di pensare, ma il Lean Thinking non è un programma.
Durante la formazione si acquisiscono le metodologie che si ritengono utili e, una volta terminato l’iter formativo, si pensa di aver compiuto buona parte del lavoro. L’immagine riportata in basso rappresenta, ovviamente in senso metaforico, il pensiero che sottostà alla base dei ragionamenti di molti che, non conoscendo. nel profondo, le peculiarità di questo modello produttivo, le origini, il contesto in cui si è sviluppato, il percorso evolutivo di pensiero che richiede per poter essere implementato, le caratteristiche e le modalità, banalizza il tutto riducendolo ad una sorta di pacchetto di cd rom da installare nel sistema azienda, un qualcosa in più che può essere di aiuto alle persone. Le immagini riportate in basso sono emblematiche e rappresentano, in senso metaforico, i concetti sinora espressi.
Si scelgono i pacchetti di metodologie da installare, si acquistano le licenze, si scelgono con cura i pc sui quali installare il tutto e… il gioco è fatto!
Si procede con l’installazione del pacchetto Lean. Con il tempo, però, cominciano ad arrivare le sorprese…
Si preme il tasto Lean, ormai acquisito nel sistema azienda e…
…si scopre che, qualcosa, non ha funzionato…
Solitamente si passa un periodo di tempo nello sconforto, si trovano tutte le giustificazioni possibili o, in mancanza di esse, i possibili colpevoli. Ma la Lean è un’altra cosa!
Le origini della Lean.
Coniato per primo da John Krafcik il termine è stato poi ripreso, aggiungendo al termine Lean la parola Thinking dagli studiosi James P. Womack and Daniel T. Jones nel loro secondo libro “Lean Thinking: Banish Waste and Create Wealth in Your Corporation” del 1996 a seguito del loro primo libro “The Machine that Changed the World” del 1988 che rese visibile, a livello mondiale, la rivoluzione produttiva e organizzativa avviata negli anni ‘50 dalla Toyota Motor Company, azienda del comparto automotive.
In questo libro i due ricercatori hanno, per primi, analizzato e messo a confronto le performance dei sistema produttivi dei principali costruttori di automobili a livello mondiale, con la giapponese Toyota, motivando i perché riguardo la netta superiorità di della Toyota rispetto al resto dei competitors.
Dalla produzione snella al pensiero snello, il modello Toyota Production System (TSP) applicato alla mente.
La produzione snella è dunque una generalizzazione e divulgazione in occidente del sistema di produzione Toyota (o Toyota Production System – TPS), che ha superato i limiti della produzione di massa (sviluppato da Henry Ford e Alfred Sloan) applicata allora (e ancora oggi) dalla maggior parte delle aziende occidentali.
Nelle pagine del loro primo libro viene analizzato e descritto il sistema di produzione Toyota, una realtà che ha capovolto il paradigma dell’organizzazione, a tutto tondo, del comparto automotive, e che ha esportato un sistema replicabile, con gli opportuni adattamenti, non solo in una fabbrica o su una catena di montaggio, ma in diverse realtà, con l’obiettivo finale di diminuire gli sprechi e massimizzare l’efficienza e l’efficacia, ottimizzando il più possibile tutte le risorse.
Nel loro secondo libro (Lean Thinking), James P. Womack and Daniel T. Jones, approfondiscono questa “rivoluzione” che parte dal Toyota Production System (TPS), sistema produttivo creato da Taiichi Ohno (1912-1990) che per primo intuì il necessario cambio di mentalità nelle modalità operative e organizzative in fabbrica, per far fronte al cambiamento della domanda globale che rendeva inadeguato il modello di produzione di massa. La ricerca continua del miglioramento, elemento costitutivo del modello TPS, ha permesso alla Toyota di passare da una piccola realtà giapponese nel 1940, ad ottenere, nel 2008, il primato di produttore mondiale di automobili.
Una letteratura ampia ha riservato spazio al modello Lean.
A partire dagli anni ’90 sul modello Lean sono scorsi fiumi di inchiostro. Molti sono i libri attualmente in commercio, con varie declinazioni del termine: dal Lean Thinking, al Lean Management, Toyota Kata, Lean Accounting, Total Flow Management etc. Quasi tutti i testi raccontano, a grandi linee, con poche diverse sfumature tra loro, il fenomeno Toyota. Questo libro che avete tra le mani, racconta le origini ma, soprattutto descrive come evitare di commettere errori nell’interpretazione e nell’implementazione di questo modello produttivo che, a tutti gli effetti, richiede un vero e proprio “cambio di paradigma”. Tra i vari errori commessi, il più “clamoroso”, a mio modo di vedere, è nella traduzione del termine giapponese “Kaizen”, che è il nome con il quale gli orientali identificano la filosofia e l’essenza alla base del TPS. Vediamolo insieme.
Kaizen: il termine giapponese del modello Toyota Production System (TPS).
Il termine Kaizen è composto da due parole giapponesi: Kai (改)significa: cambiare, cambiamento, miglioramento e Zen (善)significa: buono, migliore. Fu Masaaki Imai che, nel 1986, adoperò questo termine per descrivere la filosofia di business, alla base del successo dell’industria nipponica, negli anni ’80, in particolare della Toyota, al punto da divenire sinonimo di Toyotismo.
Il termine Kaizen fu tradotto con “miglioramento continuo”, facendo perdere così di originalità la parola, rispetto al vero significato che sta alla base del termine. Dei due termini, sicuramente il primo, cioè Kai, è quello meno semplice da attuare. Perché il cambiamento genera sempre delle resistenze, che sono naturali e che si contrappongono al nuovo.
La novità è un passaggio che determina un punto di rottura con il passato, che si ha timore di lasciare, di abbandonare o di trasformare. Pertanto, il punto di partenza di un percorso di trasformazione di un sistema organizzativo inizia con la decisione di voler rimettere in discussione le proprie convinzioni, abitudini, modalità, sicurezze, certezze, che ha inizio con l’apertura al cambiamento. E non basta farlo una volta soltanto. Altrimenti il processo, inevitabilmente, si arresta. L’attitudine al cambiamento non può che essere un processo costante, che dura nel tempo.
Fare leva sul cambiamento.
Il termine “continuo” andrebbe quindi associato a “cambiamento”, piuttosto che a “miglioramento”. Pertanto, una traduzione più pertinente potrebbe essere la seguente: “per migliorare è necessario essere, continuamente, disposti a cambiare”.
L’apertura al cambiamento è la chiave di tutto e rappresenta l’attitudine, vincente, nel percorso di implementazione del modello. È di fatto il vero motore energetico che alimenta tutto il sistema, fornendo, costantemente, le energie necessarie per la continua crescita.
Il dipendente Toyota, ogni giorno, ha un compito: individuare un muda (spreco) e ridurlo il più possibile, in ogni momento della giornata. E tutti, proprio tutti i dipendenti dell’azienda, sono occupati, costantemente, nella ricerca degli sprechi, di qualunque tipo e ad ogni livello. Questa è la vera essenza del Toyota Production System, questo è il significato più profondo della Lean!
Alcune reminiscenze medievali nella quotidianità di ognuno.
Molto spesso all’interno delle organizzazioni si sente commentare, magari al termine di una dura e complicata giornata di lavoro, frasi di questo tipo: ragazzi, facciamo gli scongiuri, ma oggi è andata proprio bene! Oppure: oggi non è proprio la giornata giusta, la sfortuna ci ha perseguitato. Se invece è andata molto bene si chiama in causa il miracolo o la magia.
In realtà l’uso di questi termini non è da considerarsi solo un modo simpatico di gestire la quotidianità o uno stratagemma per smorzare i toni e anestetizzare le ferite, come se le giornate di lavoro fossero battaglie e i dipendenti fossero alla stregua di soldati medievali, sempre pronti a difendersi e con un nemico da combattere e annientare. A volte si ha la netta sensazione che le persone ci credano sul serio, per lo più a livello non cosciente (reminiscenze per l’appunto).
Se aggiungiamo a tutto questo i problemi del mercato odierno che è in profonda crisi, la concorrenza che, per effetto della globalizzazione, è sempre più agguerrita, la crisi politica, il tasso di disoccupazione ai massimi storici, la scarsissima disponibilità da parte delle Banche nell’erogare denaro, la gestione delle aziende è sempre più un’impresa piuttosto ardua. Ci sono sempre meno certezze e il livello di difficoltà nella gestione, rispetto alla situazione ante crisi, è nettamente aumentato. La domanda è: come uscire da questo stato di cose? A parte il voler ricorrere alla magia, c’è qualcosa di concreto che possiamo pensare di fare e con una certa urgenza? La risposta è sì, senza dubbio.
Cambiare i significati per trasformare i risultati
Partiamo dai problemi: che cosa sono in realtà i problemi? Cosa rappresentano per la maggior parte delle persone? Il problema è un evento, una situazione nuova, improvvisa o già accaduta altre volte in passato. In realtà, in origine il problema non è ancora “un problema”. È il nostro modo di interpretare l’evento che gli attribuisce il “significato di problema”. I meccanismi che ho avuto l’opportunità di osservare all’interno delle organizzazioni sono molto simili tra loro. Sovente le persone sono fermamente convinte che, dietro un problema, si nasconda necessariamente un colpevole, prendendo raramente in considerazione l’ipotesi che possa essere qualcos’altro. È anche vero il contrario: la convinzione che dietro un evento si nasconda un colpevole fa sì che l’evento venga classificato dunque come problema. C’è quindi qualcuno che si è distratto, qualcuno che ha svolto i suoi compiti con leggerezza, che non è all’altezza, che rema contro, che non è adeguato a ricoprire un certo ruolo. La dinamica del colpevole è la seguente:
- Si verifica un evento
- L’evento viene classificato come problema
- Il significato associato all’evento-problema genera ansia
- L’ansia genera stress
- Lo stress produce rabbia e nervosismo
- Individuato il colpevole gli si attribuiscono le colpe
- Nonostante si sia individuato il colpevole, la rabbia e il senso di disagio non cessano
- Nell’ambiente si produce timore, si trasferisce l’ansia, si crea malessere
- Il malessere produce sconforto
- Si perde lucidità e, oltre ad allontanarsi dalla risoluzione dell’evento, si abbassano le difese immunitarie e si può cadere vittime di mal di testa, tachicardia, asma e quant’altro, finendo poi con l’ammalarsi.
Dejavù o ripetersi di pratiche errate? La rivoluzione del Lean Thinking.
Succede talmente spesso che a volte mi capita di avere la sensazione di vivere dei “dejà vu”. Vediamo adesso un chiaro esempio del pensiero complicato e del pensiero snello. Qualche anno fa, fui chiamato con una certa urgenza dal responsabile del personale di un’azienda per la quale svolgevo l’attività di consulenza Lean. In uno dei due cantieri pilota che erano stati attivati, una pressa ad iniezione aveva preso fuoco. Erano nel panico più totale. Quella pressa rappresentava la loro sfida. All’inizio, prima del cantiere Lean, era un disastro. Quando era diventata una “bomboniera” e l’efficienza era schizzata in alto, aveva preso fuoco! Ricordo che andai lì di mattina intorno alle undici ed incontrai il capo reparto con le lacrime agli occhi. Passai circa due ore con lui e i suoi collaboratori per cercare di comprendere cosa fosse accaduto. Dopo pranzo fui invitato alla riunione straordinaria, indetta dal direttore di stabilimento.
C’erano quasi tutte le funzioni rappresentate: responsabile di sicurezza, sindacalisti, personale, manutenzione, capo reparto ecc. Il direttore di stabilimento esordì così: dai su ragazzi, sappiamo che questa pressa si incendia almeno due volte l’anno. Siamo ad aprile, si è incendiata per la prima volta ma, in fondo, non è accaduto nulla di così grave, per fortuna! Trascorsero due ore da panico. Il problema, secondo tutti loro, era che gli operai non avevano indossato i DPI (dispositivi di protezione individuale) per spegnere l’incendio.
Pensiero snello e soluzioni semplici con il Lean Thinking.
Alla fine, la decisione fu di avvicinare a cinque metri dalla pressa l’armadio dei DPI che prima era posto a circa 50 metri. Tutti soddisfatti dal buon esito della riunione mi chiesero di raccontare cosa avevamo visto in reparto. Il mio discorso durò 2 minuti circa. Presentai una slide che mettemmo a punto con il team leader di progetto. La slide era animata da quattro fotografie (vedi foto in basso).
Nella prima si vede un tirante che si è rotto. Questo tirante reggeva una scodella con dentro l’alluminio fuso. Nella seconda e nella terza foto si vedevano la scodella inclinata da cui era fuoriuscito l’alluminio che, incontrando dell’olio alla base della macchina, aveva prodotto una scintilla e poi una fiamma. La fiamma, alimentata dall’ossigeno contenuto nell’impianto di aspirazione fumi, illustrato dalla quarta fotografia, aveva alimentato le fiamme e l’incendio si era propagato velocemente a tutto l’impianto. Quel tirante costava all’epoca 12,36 €. Lo avevano cambiato sette volte in un anno. L’ultima volta, quella prima dell’incendio, a febbraio. Nelle due ore trascorse in reparto con il responsabile, abbiamo contattato un’azienda poco distante dallo stabilimento che costruiva sistemi di alimentazione per presse. Erano venuti prima del pranzo a fare un sopralluogo ed avevano detto di aver già risolto problemi analoghi presso altre aziende. Dovevano cambiare il sistema di alimentazione in modo da non sollecitare più il tirante a taglio ed avrebbero anche cambiato il materiale con cui era costruito il tirante. Al termine del mio discorso ci fu il silenzio più totale.
L’importanza di analizzare i fatti in loco per analizzare i problemi e trovare le soluzioni.
Cosa c’è di diverso in questi due significati attribuiti allo stesso evento? Sono passati circa otto anni dall’accaduto. Ovviamente, dopo la modifica la pressa non si è più incendiata. La ricerca del colpevole (significato) non avrebbe mai potuto produrre la risoluzione definitiva del problema. Cercare di comprendere cosa è successo, fare domande, per poi porvi rimedio, magari costa più fatica perché bisogna andare in fabbrica, sul genba (termine giapponese che significa “luogo dove accadono le cose”), dove c’è rumore, caldo, cattivi odori e quant’altro, però ha molte più probabilità di successo. Di esempi come questo ce ne sarebbero una valanga. Tutti diversi come tipologia di problema ma accomunati dallo stesso significato/meccanismo.